
Our processes
The manufacturing of PIC and MEMS based modules involves a multitude of production processes, such as wafer dicing , die polishing, die bonding, fiber attachment, wire bonding, and many more. Below is a description of the manufacturing processes and engineering services that PHIX applies to our packaging and assembly activities.
These manufacturing steps and engineering services are also available to you separately as contract manufacturing.
Wafer dicing
Our machines can be outfitted with blades for dicing silicon, glass or ceramic wafers and panels. Application-specific blades for optical facets (suitable for known good die selection) are also available.
Die polishing
After dicing, the facets of PICs are often not smooth enough for low-loss coupling to other optical components. Our die polishing facilities ensure that the surface roughness of your chips is suitable for packaging. We use our single chip polishing machine for prototype projects and have a multi-chip machine for volume manufacturing.
Flip chip / die bonding
We have facilities for both manual and automated die bonding or flip chip assembly. The applications of this process include securing bare dies to a submount, vertically integrating PICs of different materials, and assembling components such as VCSELs, TIAs, ASICs, or photodiodes to the PIC. Our bonding methods include thermocompression bonding, soldering and adhesive bonding.
Hybrid assembly
Fiber attachment
3D printing of microlenses
Using our Nanoscribe Quantum X align tool, we can 3D print microlenses onto fiber arrays and PIC gratings with high precision. The lens arrays can focus or collimate the light, enabling mode field conversions or large distance free space coupling.
Wire bonding
Glob top dispensing
Hermetic sealing
PCB layouting and design
Mechanical and thermal design
Testing and measurement
Using optical backscatter reflectometry (OBR) we can identify losses along the light path of your module. Not only can we measure the magnitude of any reflections or attenuations, but we can also pinpoint exactly where they occur.
Our pull-shear testing equipment helps us optimize our wire bonding processes by locating and analyzing weaknesses in the bonds. We can also test the shear strength of the connections of small components like VCSELs and NTC thermistors.
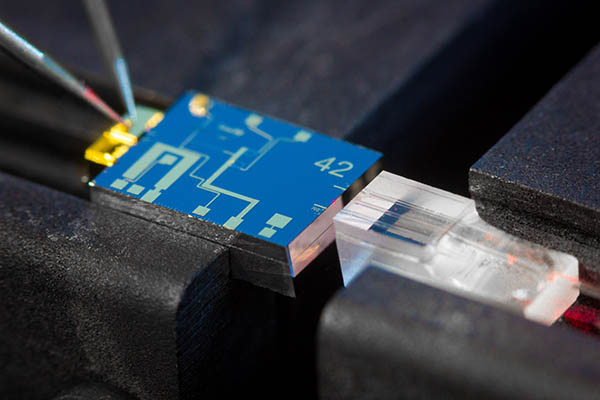
The services in which we apply these processes are: