
Market: LiDAR
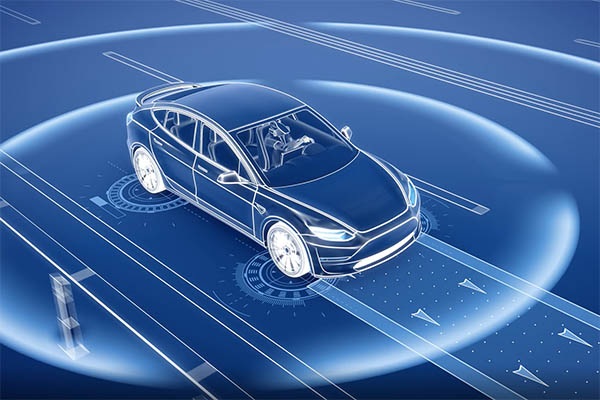
Light detection and ranging
LiDAR stands for Light Detection And Ranging and is the optical equivalent of radar. It offers a high level of detail and the ability to extract a large amount of information from the environment. A few of the best known applications are in biometric scanning, autonomous vehicles, 3D landscape mapping, and industrial security. The global market for LiDAR technologies is expected to grow from $3.1 billion in 2020 to $8.7 billion by 2025 with a compound annual growth rate (CAGR) of 22.7% for that period*.
Evolution of LiDAR
LiDAR is based on time-of-flight (ToF) measurements, where the distance to an object is calculated from the time it takes for the light to bounce back from it. At the telecom wavelength of 1550 nm powerful LiDAR systems are possible that can see through fog and are safe for the eyes. For application areas involving high speeds or uncontrolled environments, such as autonomously driving consumer vehicles, more advanced forms of LiDAR are in development. Frequency modulated continuous wave (FMCW) LiDAR makes use of the Doppler effect to quickly determine the velocity of objects in the scene, which makes it easier to interpret busy environments. Other innovations include incorporating reflected light to see around corners and using polarization data to perform material classification, distinguishing people in the scene from other objects.
Integrated photonics advantages
Photonic integrated circuits (PICs) are a great basis for LiDAR systems, because of their high number of complex building blocks, small size, low power consumption, and low cost. PIC-based narrow linewidth tunable lasers are powerful but safe light sources with the accuracy and tunability needed for FMCW operation. Solid state scanning components like optical phased arrays (OPAs) remove the need for bulky, fragile, and expensive moving parts. Tiny detectors can be integrated with the photonic IC through flip chip assembly. Together, these components provide robust high-performance systems suitable for affordable volume production. With several PIC-based prototype modules already in existence, a widespread deployment of this technology in the automotive industry is on the horizon.
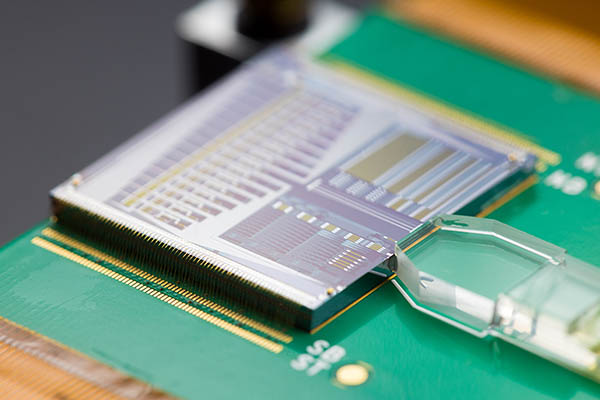
LiDAR module based on integrated photonics, packaged by PHIX
Integrated photonic IMUs
Another important component of an autonomous driving system is the Inertial Measurement Unit (IMU). Whereas a LiDAR system analyses the world around a vehicle, the IMU measures the position and acceleration of the vehicle itself. IMU systems that integrate the necessary accelerometers and gyroscopes on a single photonic integrated circuit (PIC) are currently emerging, paving the way towards robust and low cost solutions for the automotive industry.
Photonics packaging challenges
It’s important to realize that a PIC in itself is not yet a functional product. Assembly and packaging, which is the core activity of PHIX, involves coupling PICs to other chips, electronics, optical fiber (arrays), micro-optics or other components. Mechanical stability, thermal management, and affordable manufacturability are also important factors. For LiDAR systems, common photonics packaging challenges are the following.
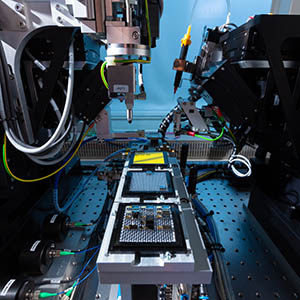
Hybrid integration
Like many applications of integrated photonics, PIC-based LiDAR systems can benefit from combining the strengths of several material platforms. An example are narrow linewidth tunable lasers with an indium phosphide (InP) gain section coupled to a silicon nitride (SiN) tunable cavity. This hybrid integration produces high performance light sources suitable for automotive FMCW LiDAR.
PHIX has extensive experience performing edge coupling of multiple PICs on semi-automatic equipment with a placement accuracy of 250 nm and active alignment to ensure process control. The resulting high coupling efficiency is critical for LiDAR systems, where every photon counts in achieving optimal long range performance.
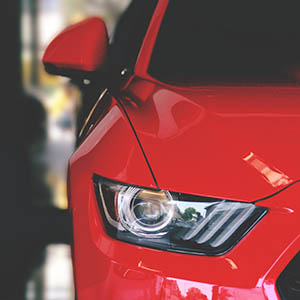
Automotive qualification
The automotive industry places high demands on reliability, energy consumption, and robustness of subsystems over a wide range of environmental conditions. PIC-based systems already benefit from low power consumption and low electromagnetic interference and enable a robust architecture without any moving parts.
Using thermistors and thermoelectric coolers (TECs), PHIX can control the PIC at a stable temperature throughout a large range of environmental conditions. A vibration resistance of up to 30 g was recently demonstrated for a hybrid laser module packaged by PHIX.
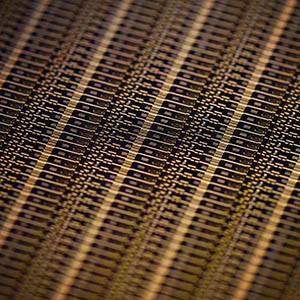
Volume scale-up
At high volumes PICs can be manufactured at a very low cost, but the price of the complete optoelectronic module is dictated mostly by the packaging process and the bill of materials. These costs can be minimized by taking manufacturability into account already at PIC design level and defining assembly processes and components with volume manufacturing in mind. PHIX is happy to support your design process at an early stage and to help define a roadmap towards cost-effective volume production.
How PHIX can support you
PHIX is happy to assist in your journey towards a successful PIC-based LiDAR module. If you are just setting out, our prototype packages are a great way to start characterization your PIC and/or its corresponding optoelectronic module. If your production numbers are starting to increase, check out our offering for volume packages. Even if the production of your modules has already begun, we can support (part of) your manufacturing by running your processes on our automatic machines through outsourcing or second-sourcing. Follow the latest developments of PHIX in our news section.
“We are working on LiDAR technology and PHIX is doing a good job at performing the many complicated assembly steps for the most critical component of our system. When there are challenges, as is normal with new cutting-edge technology, we value PHIX’s open, constructive, and solution-oriented response.” – Aditya Maheshwari (Scantinel Photonics)
I have a different question
* Source: BCC Research